D2FS Student Handbook
This guide provides an overview and orientation to the D2FS facilities, equipment, policies, and safety guidelines. All students must review this guide and sign the safety agreement prior to engagement with any shop facilities.
Table of Contents
Chapter 1: Overview and General Safety. 2
Course Engagement and Project Planning. 3
Weapons or Weapon Component Creation. 4
Chapter 2: Facilities Overview.. 5
Assembly Studio and Paint Room (2L32). 5
Chapter 3: Machine and Tool Use. 6
Chapter 5: Personal Protective Equipment (PPE). 9
Chapter 6: Digital Technologies and Fabrication Devices. 11
Chapter 7: Material Policies. 11
Chapter 1: Overview and General Safety
This guide provides an overview and orientation to the D2FS facilities, equipment, policies, and safety guidelines. All students must review this guide and sign the safety agreement prior to engagement with any shop facilities.
The Digital Design and Fabrication Studio (D2FS) is a controlled access facility. Within the facility there are seven zones—wood shop, light metal shop, electronics studio, assembly studio, paint room, laser studio, and 3D Print studio. The wood shop, light metal shop, electronics studio, laser studio and 3D print studio are supervised access zones. Students may access these zones, both undergraduate and graduate, only when an approved faculty member or the technicians are present. The assembly studio and paint room are a controlled access but unsupervised zone. Students who have received shop safety training may have unsupervised access to the assembly studio to assemble and finish their models.
Like any studio, laboratory, and machine shop at Cornell, the D2FS studio must maintain an active and robust safety program to inform and protect its users. The D2FS uses standards of safety set by both NIOSH (National Institute of Safety and Health) and OSHA (Occupational Health and Safety Administration) in the use of the facilities, materials, tools, and equipment. The rules included in this section are non-negotiable restrictions common across facilities of this type in academic and industry settings.
D2FS staff are on site to provide guidance and oversight on the safe and effective use of all tools and equipment in the facility. If you have any question or are ever in doubt about the correct operation or capability of any tool or piece of equipment, please stop all work and ask a technician.
Technical Support Staff
Technical Support Specialists at the college are here to support your technical, manual, and design questions. Get to know the staff share your excitement and plans also share what we can do to make your experience here more comfortable and successful. They are a group of highly experienced and knowledgeable staff. Meetings can be scheduled to consult with staff on your project questions or concerns by sending an email to ched2fs@cornell.edu requesting
the date and time, as well as the subject matter for the meeting. If this meeting is to have objects or items machined, 3d printed, or laser cut you should attach a copy of your digital file so that the technician can review your design, evaluate the file for production readiness, and estimate material use and cutting/printing duration. You can also get access to some information or schedule appointments on our webpage as well http://human.cornell.edu/d2fs
Should the meeting be for consultation about design, or fabrication please write a brief description of the project scope for review before the meeting. You should expect some questions from the techs about your projects finer details and problems that could occur during prototyping.
Course Engagement and Project Planning
Planning and coordinating your projects can be one of the trickiest parts of a successful project build. Many students feel the time crunch as they near the end of the semesters and their project comes due. It is important to remember that prototyping a design project is a long and complex process which needs to be thought out and scheduled well in advance of the last weeks of the semester.
The technical support staff hope to provide you the greatest possibility of success and completion of your design at the highest possible standard. The technicians are available to assist you in making a plan for your project from beginning to end so that shop time is utilized efficiently and effectively. Please take advantage of consultations with technicians to talk over design plans and review design files so that fabrication problems and machine limitations can be thought through and planned for. It is advisable to have a meeting both at the onset of your design proposal, as well as just before fabrication is to begin. These two meetings allow the techs to ask important fabrication questions, to prepare you to utilize the proper equipment safely, as well as to preschedule production times for the advanced equipment.
In addition, the technicians can provide guidance with: producing parts in a streamlined way, setting up equipment for multiple cuts, building jigs and fixtures for complicated joints and parts, choosing the appropriate tools, materials and fasteners.
Sometimes projects remain in the design phase until the final days of the semester. This delay in the start of fabrication creates a time crunch which can develop both a hazardous safety situation for you and your classmates as well as a degradation of the final design. Technicians can assist you in developing a production timeline if you are unsure on how long certain steps in your project will take. At all times, shop policies and safety and operations protocols must be followed. Deadlines and term end dates are not acceptable excuses for disregard of policies and protocols.
Etiquette and Ground Rules
Studio facilities (and all tools, equipment, and materials) are prioritized for work in support of a class or research project. Students engaged in personal projects are expected to allow students working with priority first access to all tools, equipment, and bench space.
At a fundamental level, hazardous situations can be avoided by working in an orderly and organized manner. Throughout the D2FS facilities this is an expected part of your responsibilities. No horseplay, jostling or roughhousing anywhere in the facility at any time. Tools and equipment that are setup or used shall be returned to the location or positions they were found in. Tools or parts that are damaged due to misuse or abuse will be considered a strike and/or will require the user to cover the cost of repair/replacement. Materials and works in progress shall be stored in cabinets provided or removed from site after each work session. The work area shall be broom swept and free from all tools, equipment, and materials before you leave the facility. This behavior creates a safe work environment and is polite, respectful, and time saving.
While working in the wood shop and assembly areas of the shops appropriate clothing must be worn. Close toed shoes with rubber soles, jeans or other heavy woven fabric, cotton twill shirts with rolled sleeves are all excellent examples of satisfactory attire. Flip-flops, shirts and jackets with loose sleeves, scarves, hanging jewelry are all prohibited. In addition, long hair must be tied back and secured from falling in front of face or over shoulder. If the ponytail is particularly long, it should be tied into a bun or doubled over to shorted length. If you arrive to the studio wearing inappropriate clothing you will not be permitted access.
The following basic ground rules provide for a respectful and safe environment and must be adhered to in all D2FS facilities.
- Never work along.
- Never work when impaired by drugs or alcohol or are overly tired or emotionally distracted.
- Wear safety glasses always.
- Avoid distraction – no ear buds or headphones at any time. *(unless needed for other reason please consult with staff or SDS )
- Do not let unauthorized people into the Studio.
- Please consult with staff or SDS (Student Disability Services) if any additional accommodations are needed.
- Report any injuries immediately to the shop technician.
- In case of an accident or emergency, immediately hit the safety stop button and use the emergency call box to call Campus Police and EHS.
The shop has established a three-strike rule for the violation of any shop policy or safety guideline. At the discretion of the shop technician, an oral warning may be issued in advance of a strike.
Strike 1: immediate 1 day suspension from shop; discussion with shop technician, and requirement to re-read and resign shop policy guide and safety agreement
Strike 2: immediate 1 week suspension from shop; shop technician notifies course instructor
Strike 3: immediate and permanent suspension from shop; shop technician notifies course instructor and department chair for base major.
Weapons or Weapon Component Creation
The creation or making of any weapon or weapon parts are strictly prohibited in the D2FS studios. Examples have been gravity knives, brass knuckles, and gun parts all have been asked if they could be made or experimented with in the past. All digital files will be looked over before sent to any of the digital output machines and cancelled if in violation to this rule. If you are seen making any device in violation to this rule you will receive warnings and potentially get your access to the studio revoked.
Chapter 2: Facilities Overview
Assembly Studio and Paint Room (2L32)
The assembly studio is a space that is utilized by many different departments in the college. It is both a schedule class studio and a space utilized by students for the assembly and finishing of design work in furtherance of class or research activities. Due to this multi-platform use it is required that the room be ready for any student, faculty or staff use during operating hours. All classes, and students utilizing the space must return the room to original condition at the end of scheduled time. The room is cleaned daily and any materials, projects, papers, and other items left behind and not stored properly will be removed and disposed of. Students for certain classes are assign storage lockers for projects and materials for easy access.
Assembly room hours are scheduled from 9am-4:30 weekdays. The room is open after hours with card access. If you are granted card access to the assembly room for after-hours use, you are not permitted to allow others without card access into the studio. (Some exceptions can be made for group/team projects. See technicians if you have questions.)
Use of this space requires successful completion of the training courses offered by the D2FS studios. Like the machine spaces the General Safety Rules apply to this space as well.
All chemical use is restricted to the paint room. Exceptions are non-aerosol adhesives and glues, which may be used in the room provided proper precautions are taken to avoid spills on benches and floors.
Electronics Studio (2L31A)
2L31A student assembly area has soldering stations with electronics and micro computing support. Here you can solder wires and project boards, work with Arduino and raspberry Pi, and small basic circuit projects.
- Prior to working on this bench, you are encouraged to consult with technicians about your project so they can determine the proper support that will be needed for your success.
- When soldering always make sure you are using the fume scrubber and that you never leave a plugged-in soldering iron unattended.
- Tools on this bench are to stay with the bench and cannot be taken elsewhere unless arranged with technicians. Please return the bench to the same order you approached it. All tools back to their spots and wire clippings and discards all thrown away.
- Remember working with DC or AC voltage Shorts (bare wires or exposed pieces causing poles to short out) can be dangerous so make sure your wires are covered and you are working on you project without voltage present. During testing phases when you need voltage present double check all your connections for shorts before you energize. Static mats and grounding bracelets will be provided when working with Static sensitive pieces.
- We have some test parts and circuit boards in stock these are for practice only and cannot be for your projects you must acquire your own parts for project use.
Light metal shop (2L11)
The Light metal shop can be used for the basic support in working with some metals. This room is equipped with grinders, sanders, bending, and cutting tools for light and small metal stock. There is also a small analog Bridge mill for light turning or milling. Access to this room or tools have to be requested thru the main office or emailed. No one can work in this space alone or after hours.
- Prior to working in this room, you are encouraged to consult with technicians about your project so they can determine the proper support that will be needed for your success.
- We don’t have any scrap or metal stock so you will have to plan your materials list for your project.
- Tools that are in this room stay in this room and cannot be taking out. They should be returned to the places they have been used from.
- This room is also a safety glasses required area and also no food or drink permitted.
Wood Shop (2L31)
The wood shop is a supervised area that is for support of traditional and computer aided wood working projects. This room is equipped with band saws, scroll saws, sanders, table saw, joiner, shaper, planer, CNC and many hand tools. The wood shop is accessible to safety trained individuals only during the hours when it is staffed with a technician or approved faculty.
- Prior to working in this room, you are encouraged to consult with technicians about your project so they can determine the proper support that will be needed for your success.
- Please follow all PPE and safety requirements when working in this area as well.
- Do not remove any tools from this area until you have clear it with a technician first.
- Report all tool malfunctions or odd behaviors when using any tool to the technicians
- There is scrap material available for use with your projects please see technician before removing any material from stock room to make sure it is available to use.
- This is a shared space so please make sure all tools and materials are returned to their spots and areas are free for the next person to use.
Chapter 3: Machine and Tool Use
The tools and equipment in the shop are here expressly for your use in support instructional and research activities. Each tool and piece of equipment have specific use protocols and safety rules; however, several general rules and operational protocols apply to the use of all tools and equipment:
- Think through the entire job before you begin.
- Use the correct tool for the job and know the limitations of each machine - if you do not know, ask the technician.
- Think through your procedures before starting an operation. If something doesn’t feel right or seems strange or uncomfortable don’t do it. Ask one of the technicians for help.
- Keep all guards and shields in place.
- Ensure the work and cutting tools are clamped securely in place.
- Check the machine for correct set up and free and clear movement.
- Keep my fingers clear of the point of operation. Use push sticks and brushes for this.
- Concentrate on the work and the machine at all times.
- Do not to talk to, bump into, or otherwise distract another person who is in the process of operating a power tool.
- Keep the floor around your working are clean and free of debris.
- Portable power tools are not to be used on any of the stationary machines and should be used on benches or provided workspaces. Power cords should not interfere with others in the workspace.
- Do not to walk away from a tool until you have completed the machine operation, turned off the tool, & allowed the blade, bit, or belt to come to a complete stop.
- Clean up and properly dispose of scrap materials and saw dust generated by the operation of the power tool.
- Return tools, bits, accessories, clamps, extension cords and other items used during the power tool operation to their proper storage place.
- Brush off tool surfaces and DO NOT USE compressed air to clean off any of the tools or yourself.
All maintenance and adjustments to the equipment will be performed by a staff technician. Before making a change to the operating parts of the equipment, contact a technician.
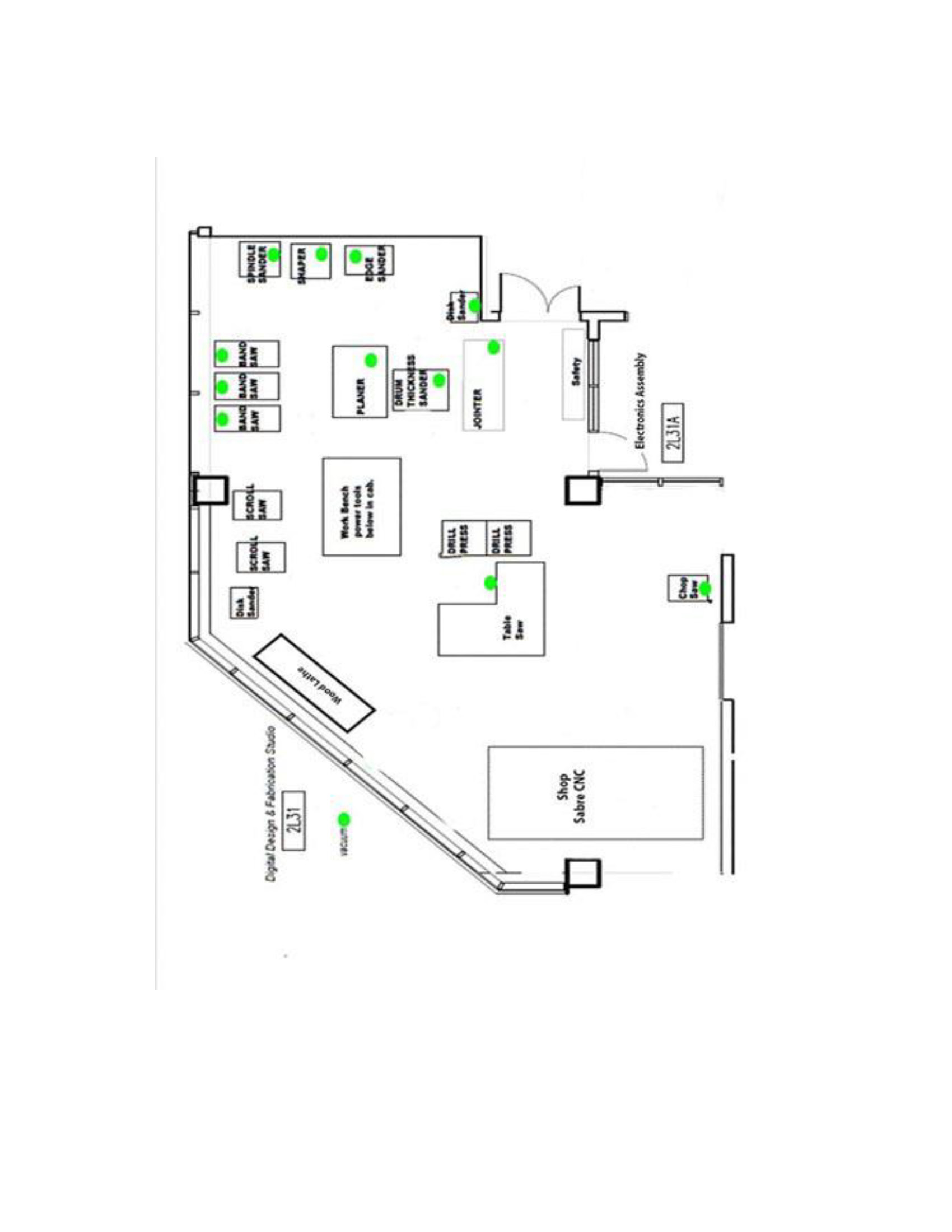
Chapter 4: Equipment List
All equipment in the shop is color code labeled by level of training required to operate the machine. Blue equipment is accessible once initial training is completed. Red Equipment requires a second level of training provided individually by shop personnel. Silver Equipment requires operation by shop personnel.
Equipment |
Training Level |
PPE Requirement |
Station |
24” Wide Drum Sander |
Blue |
|
3 |
Oscillating Edge Sander |
Blue |
|
5 |
Oscillating Spindle Sander |
Blue |
|
7 |
24” Scroll Saws |
Blue |
|
11 & 12 |
14” Bandsaws |
Blue |
|
8,9,10 |
Morticing Machine |
Blue |
|
22 |
Disc and Belt Sanders |
Blue |
|
2 &21 |
Radial Arm Saw |
Red |
|
19 |
Chop Saw |
Blue |
|
17 |
Floor Drill Press |
Blue |
|
15,16 |
SawStop 10” TableSaw |
Red |
|
14 |
6” Jointer |
Red |
|
1 |
15” Planer |
Red |
|
4 |
Spindle Moulder |
Red |
|
6 |
60” Lathe |
Red |
|
20 |
ShopSabre CNC Machine |
Silver |
|
13 |
Kern Laser Cutter |
Silver |
Laser specific glasses |
24 |
Stratasys Fortus 400 and F370 3D Printers |
Silver |
|
25
|
Full Spectrum Laser Cutter |
Silver |
|
|
Chapter 5: Personal Protective Equipment (PPE)
The D2FS provides an array of personal protective equipment for your use. Approved eye and hearing protection must be worn at all times in the facility unless otherwise indicated or instructed. This includes times where no machine or hand tool is being operated.
While not required, dust masks are also provided for your use and added protection. The provided dust masks qualify as N95 Filtering Face piece Respirator. These respirators filter at least 95% of airborne particles but is not resistant to oil. Respirators come in various sizes and must be individually selected to fit the wearer's face and to provide a tight seal. Where workers are required by employers to wear respirators, it is required to be medically evaluated to ensure that they can perform work tasks while wearing a respirator. We have provided these dust masks for voluntary use. It is required that you sign and return the Voluntary Use Form provided to you at the end of this document.
Safety glasses are provided for your use and are sterilized daily. Please make sure that glasses are returned to the cabinet as you exit the studio.
Noise induced hearing loss is a permanent hearing impairment resulting from prolonged exposure to high levels of noise. Hearing protection devices include ear plugs and earmuffs that are designed to reduce the intensity or loudness of sound that reaches the eardrum.
Earplugs are small inserts that fit into the outer ear canal. To be effective they must totally block the ear canal with an airtight seal. They are available in a variety of shapes and sizes to fit individual ear canals and can be custom made.
Earmuffs fit over the entire outer ear to form an air seal, so the entire circumference of the ear canal is blocked, and they are held in place by an adjustable band. Earmuffs will not seal around eyeglasses or long hair, and the adjustable headband tension must be sufficient to hold earmuffs firmly around the ear. Earplugs must be snugly sealed so the entire circumference of the ear canal is blocked. An improperly fitted, dirty or worn-out plug may not seal and can irritate the ear canal. Properly fitted earplugs or muffs reduce noise 15 to 30 dB. The better earplugs and muffs are approximately equal in sound reduction, although earplugs are better for low frequency noise and earmuffs for high frequency noise. Simultaneous use of earplugs and muffs usually adds 10 to 15 dB more protection than either used alone. Combined use should be considered when noise exceeds 105 dB. If there is a preexisting hearing loss or if you have hearing aiding devices, please work with us or SDS* to make sure we fit you with an appropriate solution for your protection.
A good "rule of thumb" for determining if your work area or activity requires hearing protection is your ease or difficulty hearing or understanding a "normal" tone of voice at about three feet. Greater difficulty indicates that noise levels are exceeding safe levels and you should be using hearing protection.
According to the National Institute on Deafness and Other Communication Disorders, frequent and extended exposure to sound pressure in excess of 85 decibels can cause long-term hearing loss. Data shows that many activities and tools require the use of hearing protection. This includes, but is not limited to, lawn mowers, tractors, leaf blowers, weed trimmers, chain saws, concrete saws, concrete/hammer drills, snow blowers, power saws, backpack vacuums, working near running chillers, etc.
85 Decibels (dB) - the "Action Level" where hearing protection is required.
90 dB - the OSHA, 8-hour average exposure limit.
100 dB - exposures longer than 15 minutes are not recommended.
110 dB - regular exposure of more than 1-minute risks permanent hearing loss.
Headphones, ear buds, noise cancelling headphones are not permitted in the shop without special permission from the technical support staff and SDS. Personal music players are not a form of hearing protection. Many MP3 users listen at much higher levels - often without realizing the risk. Some personal music players can reach more than 115 decibels, representing significant potential for damage in a matter of a few minutes.
Chapter 6: Digital Technologies and Fabrication DevicesSoftware
The following software is in use and acceptable by the studio equipment. Technical staff are not trained to instruct on use of the applications.
|
|
|
Adobe Illustrator |
|
|
|
|
|
|
|
|
|
|
|
Laser Cutter
Two lasers are available. The Class 4 laser is a fast and powerful, large scale open bed machine employed for most finish projects and materials under a half inch thick. The Class 3 laser is a smaller, self-contained unit employed for prototyping and materials X. Laser cutting is achieved by burning through material, and thus requires specific safety protocols and 100% supervision (i.e. the laser should not be operated without somebody physically in the room monitoring the entire process). The following operating procedures guide the use of the laser cutter:
• The technicians will determine whether a material can be safely cut. Most common materials have been reviewed and evaluated based on flammability and the toxicity of fumes generated in the burning process. See the posting in the laser cutting studio. Before cutting or engraving any new materials, MSDS Safety Data Sheet for that material will be acquired to verify the product is safe to cut or engrave without generating toxic fumes.
• Protective eyewear will be worn by all personnel in the laser room, whether the machine is operating or not. Direct eye contact with the laser will cause serious eye injury and could cause blindness.
• A CO2 fire extinguisher is in place within easy reach of the person(s) monitoring the job.
• Ventilation systems will be checked before any job commences to ensure that it is operating correctly.
CNC Router
One CNC (computer numerical control) router is available. In response to a digital design, this device uses servo motors to manipulate a router through up to five axis of movement along a path designed to carve out material. This machine requires advanced technical knowledge and thus solely technician operated. It is advised that you seek technician’s assistance in the early stages of planning a project to ensure your design files are ready for production on the machine. The following operating procedures guide the use of the CNC:
- The technicians will determine whether a material can be safely routed. Most common materials have been reviewed and evaluated. The Technicians have a list of materials and their routing status.
- Ventilation systems will be checked before any job commences to ensure that they are operating correctly.
- The Technicians will set-up and start all projects, and will allow monitoring by the person working on the project.
3D Printers
Three 3D printers are available. Our large Stratasys Fortus 400 and F370 are industrial grade, production printers. They are completely automated and is on par with the best printing technology in the business. The LutzBot Taz 5 located in the assembly room (2L32) in comparison is a desktop machine that is widely available on the consumer market. This printer is open to use for those with access to the assembly room. These machines offer a wide range of capability and technology. A consultation meeting with the technicians is required during which your file evaluated, and the print scheduled.
Chapter 7: Material Policies
The D2FS provides a wide array of material goods for the facilitation of your projects. Certain categories of material are available for use free of charge while other specialized materials are available for purchase by charge to your Bursar account. Price lists reflect average market rate and are generated each semester but are subject to change throughout the year as market rates fluctuate.
Should you need a specialty item or are having trouble finding hardware, or are developing an idea for your design, the technicians are available and knowledgeable in the acquisition of materials and specialty hardware.
Materials Available for Use Free of Charge:
- Recycled wood materials
- Assorted Zinc Plated Bolts and Nuts
- Assorted Washers
- Imperial Drill Bits, Paddle Bits, Forstner Bits
- Assorted Drywall Screws, Assorted Wood Screws
Materials Available for Purchase:
- Wood
- Wood Composite Materials
- Acrylic Sheet
- Cardboard
- Chipboard